Engineered Planning
Whether it's a single unit or full plant turnaround, successful chemical decontamination begins with thorough planning prior to execution. Our team of experts with operational experience collaborates with you to create a custom solution – chemistry, procedures and staffing – for the entire timeline of the decontamination process.
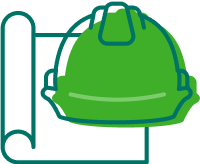
We Plan To Succeed
One of the main reasons a turnaround can run behind schedule is because of delayed decontamination and unit handover. The most common cause for this is? A lack of planning. And that lack of planning costs you time and money.
At ZymeFlow, we solve that problem by immersing our planning team into your turnaround process as early as possible. This process begins with an on-site project assessment and concludes with a project debrief upon the successful completion of your turnaround.
Communication, thoroughness and accountability on our part, will result in greater reliability and safety, will reduce shutdown time and decrease overall costs. Throughout the process we are onsite as a professional presence, to be the subject matter experts and to collaborate with your operators for the best results.
Our planning process:
- Decreases costs through chemical optimization
- Trains operators on decontamination procedures
- Integrates into normal refinery procedures
- Reduces chances of recontamination
We’ve Got Decontamination Planning Down To A Formula
Site Visit and Kickoff
Once you select ZymeFlow - the process begins. Most engagements start with a site visit to review your turnaround goals with your team. Once we have the lay of the land, we move onto the development of the plan.
Site Visit Steps Include:
- Kickoff and scope overview
- Walk down associated equipment
- Development of decon path and procedures
- Identify injection, drains and vents
Plan Development
This phase involves detailed planning and scheduling. We'll draft and submit preliminary drawings and guidelines for client approval. As true collaborators in the process, we welcome your input, direction and revisions as the planning manual is developed.
Planning Manual includes:
- Drawings broken down by circuit
- Chemical decontamination procedures
- Chemical injection tag list
- Detail mechanical listing
- The safety matrix
- SDS's
Planning Finalization
Upon approval of the planning manual our team will assist with operational training, MOC review or plan review as requested by the facility. At the appropriate time, our planners will affix injection and drain tags in the appropriate locations.
Finalization Includes:
- Operator training
- Injection and drain tagging
- Execution kickoff
ZymeFlow Planning In Action
ZymeFlow and a refinery in Greece started discussing decontamination strategies for a planned turnaround for several units, including crude units, two vacuum distillations units, visbreaker, and Tertiary Amyl Methyl Ether unit. Returning for the eight time to the refinery, ZymeFlow returned ready to decontaminate.
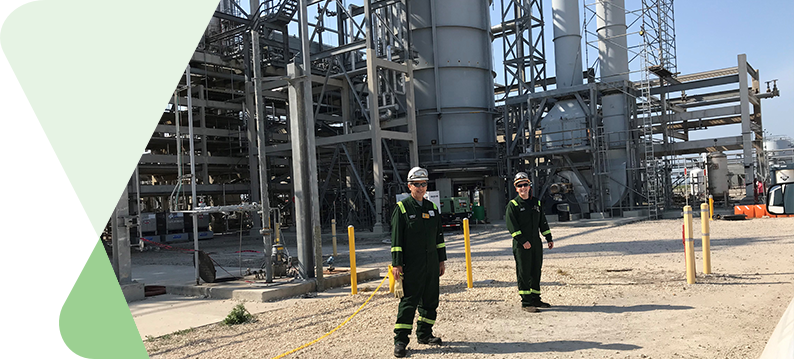
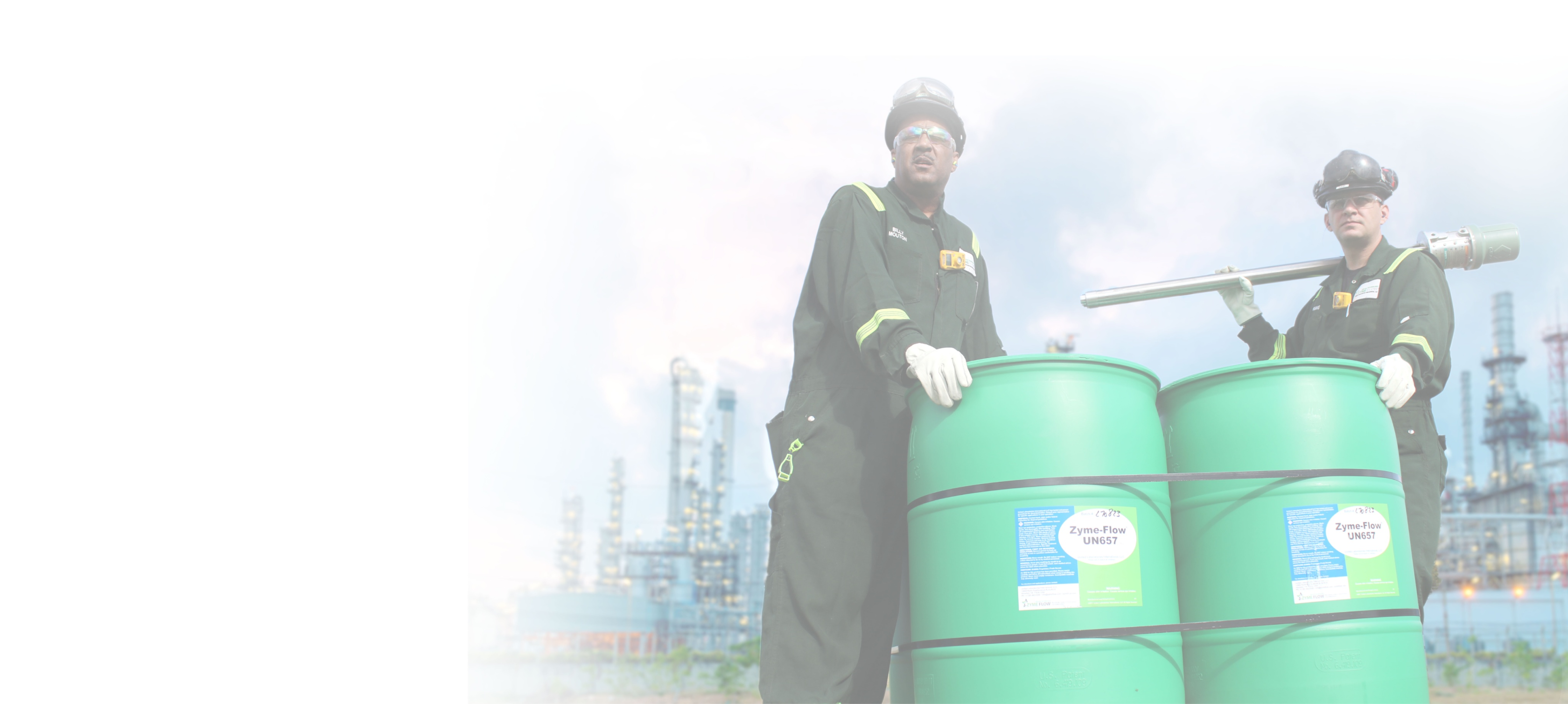
Let's get started.
A successful chemical decontamination begins with a thorough, custom plan created far before the job begins. As the undisputed leader in the chemical decontamination industry, we embed with you to provide custom solutions and consistently outperform our competitors. We listen. We collaborate. We deliver.